Howard Haselhuhn
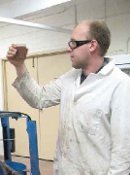
- BS Chemical Engineering 2010
- MS Chemical Engineering 2013
The ASISC research center at Michigan Tech is a partnership of academic institutions
and industry with interests in mineral processing. Members pool resources to address
a diverse spectrum of interdisciplinary research questions. Their primary goal: to
develop a new generation of sustainable, economical mineral processing technologies.
PhD student Howard Haselhuhn is an ASISC researcher focused on water chemistry. At
an iron-processing facility, he recently studied the technology used to remove impurities
from iron ore.
Depending on the time of year, almost all of the water used in an iron concentration
plant is recycled. “This is not just important from an environmental standpoint; it
is cost effective to conserve the thermal energy in the process water as well as the
water quality within the plant,” explains Haselhuhn. “Iron ore concentration facilities
depend on surface chemical interactions for many concentration operations; therefore,
strict control of water chemistry is necessary. Most tap water is of insufficient
quality for direct use within iron ore concentration plants,” he notes.
Iron ore is ground down into very small particles, which are mixed in water. Reagents
are added to the mixture to flocculate iron oxide particles. These flocs, which contain
more iron, settle quickly, leaving unflocculated particles, containing primarily silica,
to remain suspended. However, Haselhuhn discovered, sometimes the raw ore and recycled
water contain high levels of magnesium. In turn, that causes silica particles to cluster
and settle out with the iron, rendering the separation process ineffective.
“By compensating for the excess magnesium, companies could reduce the loss of iron
in their concentration process, something that could provide millions of dollars in
potential savings,” he says. “We are fortunate enough to have an abundance of fresh
water in the Great Lakes area, which makes iron processing easier. In many other parts
of the world, the process water must at least partially come from the ocean, which
is very high in magnesium. They can still process; just with different, more expensive
methods.”
Once the ore is concentrated, it is in the form of an iron oxide. “Obviously, the
oxygen must be removed before it becomes iron,” he adds. “This is typically accomplished
by reacting it with a carbon source, typically coal. One direction ASISC has been
exploring is replacing coal with a biomass-derived reductant. This decreases dependency
upon non-sustainable natural resources.”
The mineral processing industry makes continuous improvements in technology, explains
Haselhuhn. “Many of these improvements have been small and locale-specific, but once
in a while there is a giant step forward that can bring about a new era in the industry.
These dramatic improvements will be necessary to remain a sustainable industry. Unlike
many industries, the feedstock (iron ore) is constantly degrading in quality. Eventually,
it will not be feasible to process unless new methods are developed.”
“Repurposing waste will be key to reclamation of mining sites once the ore is gone,”
he adds. “ASISC is committed to finding ‘zero-waste’ solutions to mineral processing.”
Excerpted from Michigan Tech Engineering Research 2013