Amitabh Narain
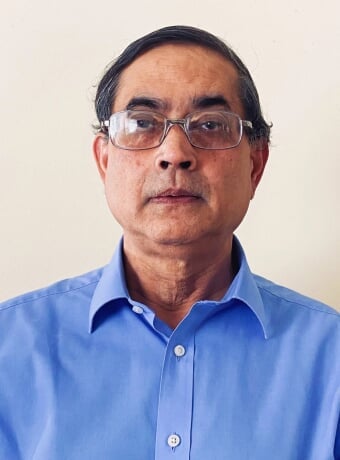
- Professor, Mechanical and Aerospace Engineering
- PhD, University of Minnesota
Biography
Professor Amitabh Narain (Ph. D., University of Minnesota, 1983) is a Professor in the Department of Mechanical and Aerospace Engineering at Michigan Technological University, USA; a Fellow of the ASME; current Associate Editor of ASME JOE, and a past AE of the Journal of Heat Transfer (2015-2021). Dr. Narain has served and continues to serve on several government funding panels and is active in several ASME committees: HTD-K8 (past Chair and Vice-chair), HTD-K13 (Member), AMD-Fluid Mechanics committee (past Chair and Vice-Chair), etc. His current research areas deal with state-of-the-art experimental and computational techniques for phase-change (enhanced nucleation flow boiling and flow condensation) which, at the system level, relate to energy technologies such as thermal management and waste heat recovery – with emphasis on electronic and data center cooling. Dr. Narain’s research has received regular funding (from NSF, NASA, industry, and gifts) covering the period of 1986 - 2023. Dr. Narain has authored over 85 peer-reviewed articles (about 40 journal articles). He is active in teaching and mentoring students (graduate and undergraduate) as well as in national/international-level professional leadership and service.
Current Research Interests
See: https://www.nsf.gov/awardsearch/showAward?AWD_ID=2327965&HistoricalAwards=false
Also:https://www.nsf.gov/awardsearch/showAward?AWD_ID=2327966&HistoricalAwards=false
Current research assists in developing novel energy systems that will effectively address next-generation electronic cooling requirements – in conjunction with improved waste heat recovery and a dedicated small-scale power generation approach for data centers.
The ongoing software side of system-level research focuses on innovative thermal system designs that combine Thermodynamics, Fluid Mechanics, and Heat Transfer. At a higher level of system considerations, these provide data-center cooling options as well as dedicated power-supply options –which show significant economic and clean energy advantages (such as some waste heat recovery into electricity, water use, and carbon footprint reductions).
Links of Interest
Areas of Expertise
- Heat Transfer
- Fluid Mechanics
- Thermal Management
- Multiphase Flows and Phase-change Phenomena
Research Interests
- Boiling and Condensing Flows
- Enhanced Nucleate Boiling (ENB) in Innovative Heat Exchangers with Specialized Flow Loop with Flow Control
- Experiments, Modeling, CFD/CHT
- Gravity-independent ENB
- Electronic Cooling of "Chips" for High Performance Computing (HPC)
- Power-Electronics Cooling for Electric Vehicles (EVs)