-
Origins of Orbion: When Preparation Meets Opportunity
Houghton is the launch pad for Orbion Space Technology, one of the brightest stars in a newly imagined space economy where small satellites are huge game changers. Research ingenuity and the right timing coalesced to propel Orbion forward following its establishment in 2016, says CEO Lyon (Brad) King, Michigan Tech's Richard and Elizabeth Henes Professor of Space Systems. King leveraged two decades of on-campus research and education to launch the off-campus company and lead the world, and perhaps the solar system, into a new space age.
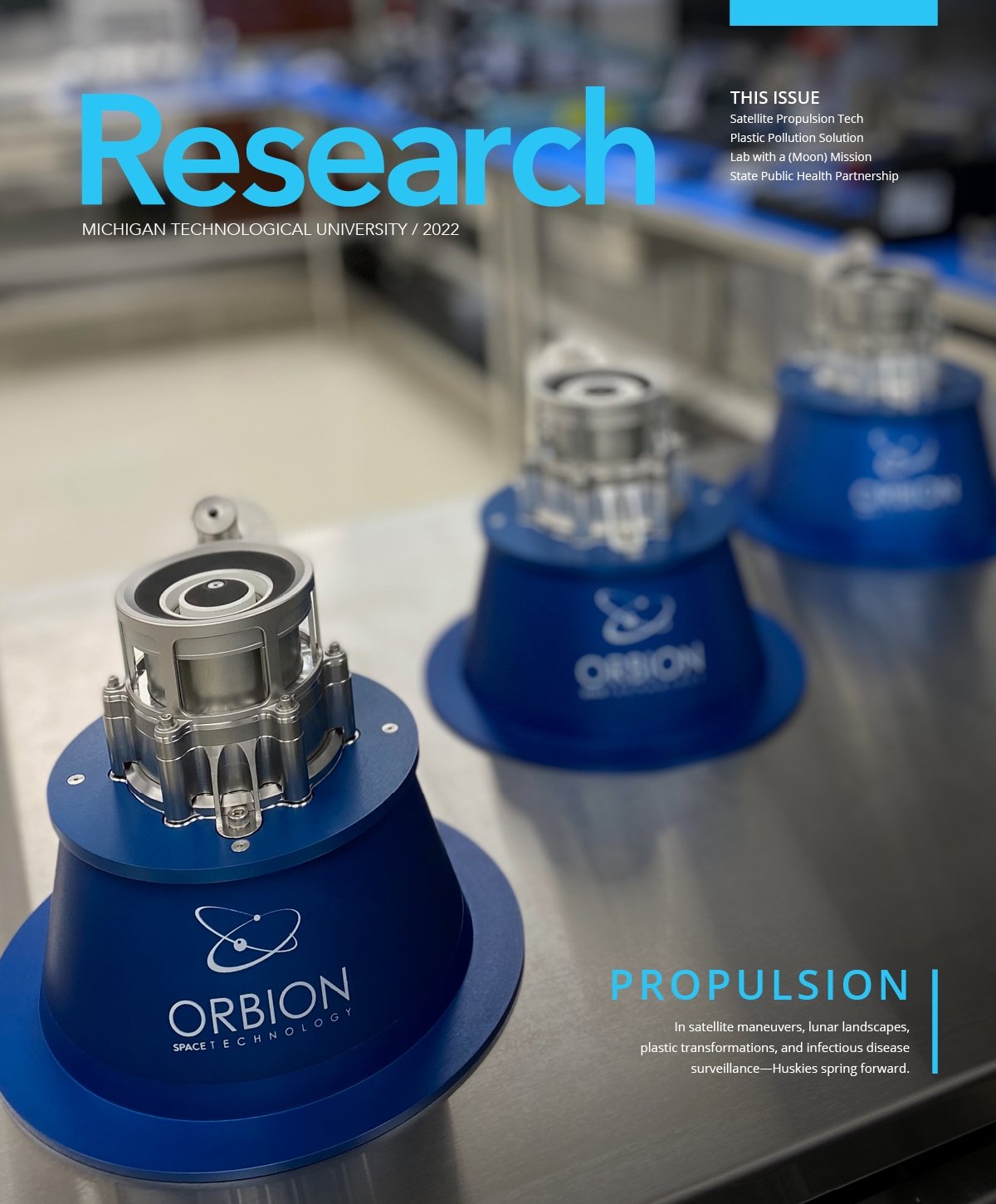
On the cover: In satellite maneuvers, lunar landscapes, plastic transformations, and infectious disease surveillance—Huskies spring forward. Image Credit: Jason Makela
Research is published by University Marketing and Communications and the Vice President for Research Office at Michigan Technological University, 1400 Townsend Drive, Houghton, Michigan 49931-1295.
- Nicole Kelly—Creative Director
- John Lehman—Vice President for University Relations and Enrollment
- Ian Repp—Associate Vice President for University Marketing and Communications
- David Reed—Vice President for Research
- Cathy Jenich—Assistant to Vice President for Research
- Natasha Chopp—Research Office
- Cyndi Perkins—Senior Content Specialist
- Jessie Tobias—Copy Editor
- Sarah Atkinson—Studio Production and Creative Manager
- Ben Jaszczak—Multimedia Specialist
- Megan Ross—Digital Support Manager
- Jen A. Miller—Freelance Writer
- Joel Van Diepenbos—Student Photographer
- Comments to the editor
magazine@mtu.edu - Address changes
gccolaro@mtu.edu
Learn more about research at Michigan Tech online.