When Ron Staley '77 '80 sees a historic building fallen into disrepair, he doesn't despair. Instead, he looks past things like rotted ceilings and floors, missing copper, and water in surprising locations, and sees opportunity. With each project he tackles, he's "taking a building apart and putting it back together for future generations."
Staley leads one of the country's most respected historic preservation teams at The Christman Company, where he's senior vice president and executive director of historic preservation. For nearly four decades, he and his team have restored architecturally significant structures, including the US Capitol and Henry Ford's estate, preserving them as cornerstones of US history.
His main project right now is a once and future marvel: Michigan Central Station. Once one of the most popular and beautiful rail stations in the US, it had fallen into such ruin that bats were living in the basement by the time Staley and his team prepared to take on its rehabilitation.
It's not an easy project—but Staley is used to tackling tough projects thanks to a work ethic that started during his time at Michigan Tech.
"Tech taught me that you need to do hard work in order to succeed," Staley said. "When I took my last exam, the thought hit me that I'd never have to work like that again. The reality is I've never quit working that hard."
Photos by The Christman Company
A Fresh Start at Michigan Tech
Staley initially wanted to be an architect. He studied architectural drawing in high school, where an instructor saw him as a better engineering candidate. He admits that he wasn't the best high school student, but a classmate a grade older than him had gone to Michigan Tech, and it seemed like a good fit. (Both of Staley's younger brothers thought so, too—all three attended Tech, though five-year age gaps kept them from studying together.)
Staley applied for the two-year Associate of Applied Science in Civil Engineering Technology degree. His uncle, also a civil engineer, told him he would need more than just technical skills to excel in his career. He encouraged Staley to continue at Michigan Tech and earn a Bachelor of Science in Business.
While at school, Staley was president of the MTU Aquanauts scuba diving club and Management Club, and did part-time drafting work for an engineering firm in Hancock. After graduating with his BS, he was recruited by the Bechtel Power Corporation. One of his first projects out of college was cost scheduling a $1.4 billion power plant.
"I give Michigan Tech a lot of credit. The tools they gave me, especially on the business side, set me up for this career. At this point, there's just so much I want to give back. I want to ensure that the next generation will be inspired and prepared for whatever comes next."
After four years at Bechtel, he was presented with an opportunity to work on a sewage plant in West Chicago, Illinois, which wasn't appealing to him. Staley had just gotten married, and he and his wife's first baby was on the way; their growing family wanted to stay in Michigan. The Christman Company had been one of Bechtel's subcontractors. "I made a phone call to the president and said I think it might be time to talk," he said.
Staley joined The Christman Company in 1984. By 1986, he'd begun leading his first historic project: the total restoration of the Michigan State Capitol. Originally opened in 1879, the building took six years and $58 million to restore. It was a complicated job because of the building's age, lack of upkeep, and prior misguided renovations. The building also needed to stay open throughout the phased restoration process.
Challenging? Yes. But an unmitigated success. When completed in 1992, the Michigan State Capitol was designated a National Historic Landmark and won numerous national awards.
The project made Staley and his 13 direct reports experts in historic restoration—and through their work, the team met some of the country's highest-profile preservation architects, most based in New York and Washington, D.C. So, Staley asked Christman's president, Phil Frederickson (a fellow MTU grad), if the company might want to "take experience and put it on the road."
The company directed Staley to lead a market study to determine whether a business case existed for the work. The answer was a resounding yes. A detailed business unit plan followed, and Christman soon created a national historic preservation division, opening a new office in the Washington, D.C., metro area.
"My uncle was absolutely right about taking business classes," Staley said. "They were extremely valuable to me when we expanded."
Finding a Future in Repairing the Past
When Staley started at Christman, the company did $30 million worth of business per year. Now it's over $1.4 billion. Staley has led building restorations all over the world, encompassing over 35 National Historic Landmarks, 77 properties on the National Register of Historic Places, one national memorial, one national monument, and two UNESCO World Heritage Sites.
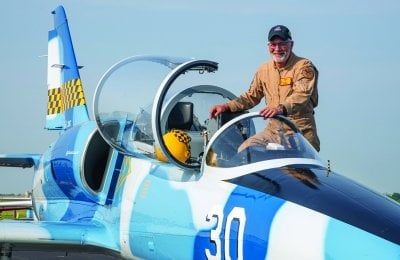
These include projects with unique value to US history—like the Virginia State Capitol, designed by Thomas Jefferson. It required not only a complete rehabilitation, but also construction of an underground visitor center without disturbing the original building's foundation.
"A lot of my classes at Michigan Tech in subjects like soils and structures proved to be very important on this project and others," Staley said.
The company also completed multiple restoration projects at the US Capitol, including restoring the base of its famous dome and constructing the podium and grandstands for the last four presidential inaugurations.
The restoration of the Main Administration Building at the University of Notre Dame, known as the Main Building or the Golden Dome, also included preserving a historic dome—but one with a less-than-uniform design. Technically the university's second administrative building, it was put up quickly after a fire destroyed the original in 1879, and consistency in construction was sacrificed for speed.
"When we got into the building, we found that in each wing the structural configuration was totally different," Staley said. "One had beams going north-south, and the other had them going east-west. If one had two-by-twelves, the other had two-by-tens. It's not uncommon in our historic preservation work to find everything that's hidden, and boy, did we have a lot of hidden surprises in there."
Michigan Central Station isn't the company's first partnership with Ford, either. Fair Lane, the Henry Ford Estate, is a 1,300-acre estate in Dearborn, Michigan, built in 1914 for Henry and Clara Ford. After they died, it was largely abandoned, then gifted to the University of Michigan-Dearborn in 1957. The university initially used it for storage.
When Christman got to it in 2007, the estate was in rough shape. Insulation had been sprayed into the attic, despite leaks in its historic clay roof—which caused the roof to rot and collapse. Christman restored the roof, adding a new ventilation system and replicated copper gutters, flashing, and trim. They have also continued restoration work on the building itself, as well as the mansion's original swimming pool room and a six-level powerhouse—a collaboration with Thomas Edison that still contains all the equipment that made Fair Lane self-sufficient in power, heat, and light.
"I've always valued our historic preservation clients and those relationships, and the opportunity to continue doing work for them," Staley said.
A Grand Old Rail Station Fallen to Ruin
Michigan Central Station opened in 1913 at the peak of rail travel's popularity. Known then as Central Depot, the 650,000-square-foot station was the tallest in the world, boasting a three-story train depot and 18-story office tower. The building's prominence was bolstered by its location in Detroit, a city ascending as a global leader in industry and innovation.
During World War I, the station handled 200 trains a day. By the 1940s, a bustling crowd of 4,000 passengers visited every day, and 3,000 employees worked in its office tower. The station counted Theodore Roosevelt, Franklin D. Roosevelt, Harry S. Truman, Charlie Chaplin, and Thomas Edison as famous visitors.
But by midcentury, as car travel boomed, Michigan Central Station fell into disuse. In 1967, the waiting room closed and its walnut benches were sold off for $25 each. The last Amtrak train passed through in 1988. When Staley first visited in 1993, the station had been bought out of foreclosure by Controlled Terminals Inc. A renovation was planned—but never happened.
"There were holes where the elevator motors had rolled off the tower roof and blown through the floors below," Staley described, adding that the state of the building wasn't the only reason to be concerned. "The guy showing us around had a gun."
It was a far fall from grace for a building once touted as a paragon of Beaux-Arts splendor in the landscape of American architecture.
Staley went back in 2018, after Ford acquired the building and began investing $740 million in restoration. By that time, the station's condition had gotten exponentially worse.
His team counted more than a thousand holes in the floor where piping had been ripped out or whole sections had collapsed. They found 2.5 million gallons of water in a sub-basement they hadn't known existed, and up to six feet of ice on parts of the roof structure, which was also missing all its original copper. There were no lights or heat, and debris was everywhere—including asbestos.
"One of my exciting days was when things started to warm up," Staley said. "I walked in the basement and woke up the bats."
Nothing could dissuade Staley and his team, however. They saw it as the perfect challenge. "We were pretty geeked out," he said.
Resurrecting and Modernizing Michigan Central Station
Restoration was no easy task. They started at the bottom, in the sub-basement.
"This building probably had water problems since the day it was built," Staley said. "But this particular flooding was mainly caused by scrappers. During the years the building was abandoned, scrappers had removed the historic copper roofing on the waiting room, shattered the glass skylight over the concourse—and also the majority of the building's windows—and removed most of the cast-iron stormwater collection system within the building. So, essentially, every time it rained, water flowed to the basement. Snow would also enter in the winter, then melt come spring."
The uncontrolled moisture in the building was the largest single cause of structural damage, Staley said. His team drained the water using a series of pumps, running the water through filters on its way to the sewer system. (The water was tested before filtration to ensure no hazardous materials would enter the sewers.) They then set about repairs to keep the building dry.
From the basement they worked up, dealing with COVID-related delays and supply chain disruptions while finding creative solutions to each new challenge on every floor. They installed heating, cooling, and mechanical systems in the space once occupied by railroad tracks, operating equipment, and trains—equipment that now includes nearly a thousand fan coil units. They also added more than 1.5 million feet of electrical wire and cable throughout the building, along with 10 miles of fire suppression pipe, 4,500 sprinkler heads, emergency stairs, and new elevator systems, bringing Michigan Central Station up to modern safety standards.
"The grandeur of the interior is something that will be lasting, for it is of marble, brick and bronze, all of this is set off by one of the best lighting schemes ever installed in a building."
Staley knows that in his line of work, it's the small details that make a great restoration—even if the average visitor will never know how far the team went to make the project as historically accurate as possible.
For example, decades of water freezing and thawing had cracked most of the building's limestone and created leaks, causing the stone to erode. To replace it, Staley's team could have purchased stone from the most convenient supplier. Instead, they went to the original limestone's source: Indiana's Dark Hollow Quarry, which closed in 1988. In a stroke of luck, quarried blocks were found in a nearby forest, surrounded by 30-year-old trees planted before quarry operations ceased. Christman took the extraordinary step of reopening a closed forest road so the blocks could be retrieved. That long forgotten limestone is now a central aesthetic feature in the restored station, in everything from decorative column bases to sections of railing.
This project also involved the cleaning, restoration, or replacement of more than 29,000 Guastavino terra-cotta tiles. Tiling by Spanish architect Rafael Guastavino is found in monuments and landmarks across the US, from the Boston Public Library and the Grand Central Oyster Bar and Restaurant in New York to the famous registry room at Ellis Island. "Guastavino tile domes are very unique structures from the turn of the 20th century," Staley said. "Michigan Central is the largest example of Guastavino tiling in the state of Michigan and one of the most complex in the country, according to our team's structural engineer, due to the system being supported by a complex structural steel frame system."
Staley said every single tile had to be sounded, or checked to make sure they were securely attached to the ceiling. Those that weren't were reaffixed with thousands of stainless steel pins and 8.6 miles of historically correct mortar.
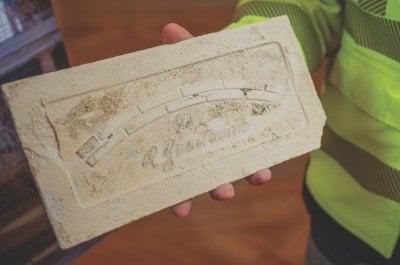
"Three of my previous projects had Guastavino tile systems we restored, but Michigan Central was the first project where the tile was found to be actually stamped with the Guastavino dome logo. For our historic preservation team, this was like being able to touch a Picasso painting." —Ron Staley '77 '80
Although cracked tiles with Guastavino's logo were not reused, they are valued pieces of construction history for Staley's team to preserve.
Their goal was for a visitor not to notice the difference between tiles from the 1910s and 2020s. If a tile couldn't be repaired, it was replaced with a reproduction made by a specialty tile maker in Buffalo, New York, who spent over a year perfecting the right textures and color range to match the new tiles with the historic ones.
Other elements, like the cast iron used extensively on the building's exterior, were created entirely anew. "While it is still possible to manufacture these cast-iron elements, as we started to 3D scan pieces to make molds, we discussed the idea to 3D print some of these elements instead, especially those that would require hundreds or even thousands of unique pieces," said Staley. His design and construction team worked with Ford's additive manufacturing team to develop prototypes, determine materials, and set the delivery schedule. "Ultimately, 3D printing ended up being a great process for manufacturing many unique detail pieces, including all the decoration around the 40-foot-tall waiting room windows and plaster ceiling detail pieces in the historic tea room and men's smoking room."
Restored, Michigan Central Station will be a 30-acre walkable innovation hub with multiple plazas and open spaces, along with 1.2 million square feet of commercial public space and offices for 5,000 employees. It will be home to a first-of-its-kind testing platform for technologies like autonomous and connected vehicles, smart roads and infrastructure, public transit, and micromobility. Taking a note from its past as a transportation hub, it will again be a key connection between a broader network of city and regional assets, with the state of Michigan aligning more than $126 million in new and existing programming and resources.
"It's just magnificent how the building turned out," Staley said. "It is a great testament to the craftsmanship our team was able to achieve to get it done."
It was also a lot of hard work—the value of which Staley first learned at Michigan Tech, where he now serves on the advisory board of the construction management and engineering management programs. He also mentors students who might be working with him on the country's next great historic preservation project.
Michigan Technological University is a public research university founded in 1885 in Houghton, Michigan, and is home to more than 7,000 students from 55 countries around the world. Consistently ranked among the best universities in the country for return on investment, Michigan’s flagship technological university offers more than 120 undergraduate and graduate degree programs in science and technology, engineering, computing, forestry, business and economics, health professions, humanities, mathematics, social sciences, and the arts. The rural campus is situated just miles from Lake Superior in Michigan's Upper Peninsula, offering year-round opportunities for outdoor adventure.