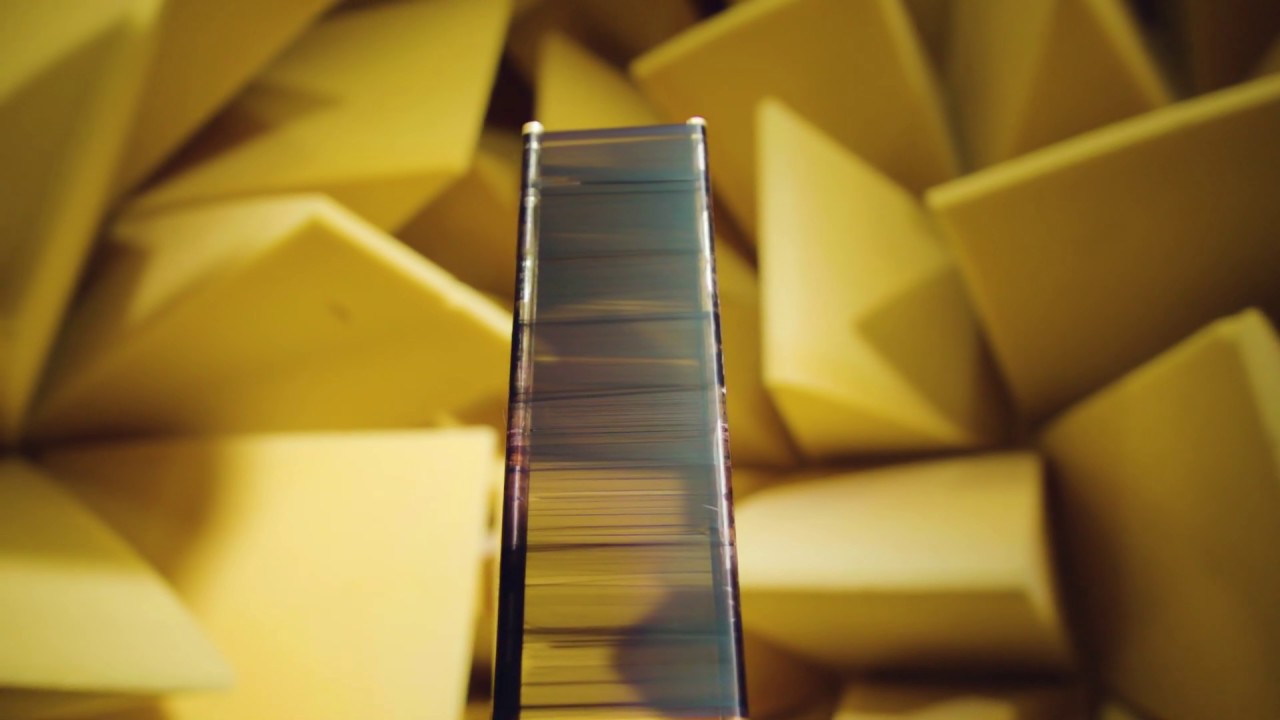
Acoustic Engineers use Carbon Nanotubes
Our students and faculty know what tomorrow needs. Acoustics engineering focuses on making spaces sound the best they can by analyzing complex sound waves, testing new materials, and building sound-cancelling devices. That matters because in places like hospitals, noisy heating and cooling units affect people’s ability to recover from illness and prevent airborne infection.
Abadi Lab
Abadi Lab at Michigan Tech is an interdisciplinary lab focusing on solving problems at the interface of materials, mechanics, and nanoscience. Our lab employs advanced manufacturing techniques such as 3D printing, bioprinting, and chemical vapor deposition to explore various engineering applications of advanced materials ranging from structural and electronic materials to tissue engineering and medical devices. A great focus of our lab is on conductive nanomaterials especially carbon nanotubes, carbon nanotube forests, graphene, and conductive nanomaterials incorporated in polymer composites.
Location: MEEM 1004
Contact: Parisa Pour Shahid Saeed Abadi
Advanced Metal 3D Printing Center
The Advanced Metal 3D Printing Center houses a powder bed fusion 3D Systems DMP Flex 350 Metal Printer. It is available for use by the campus and external communities. The printer is capable of producing parts with complex geometry from metal powders on a scale similar to industry standard.
Location: M&M 117
Contact: Russell Stein
Alternative Energy Research Building (AERB)
The AERB is a 4,000-square-foot building dedicated to alternative energy research. The all‐new facilities include a laboratory with unique equipment to study fundamental combustion and sprays; a fuel cell laboratory with an environmental chamber capable of reaching –40 degrees Celsius; and a wind flow laboratory used to study topics including the effects of variable-geometry wind turbine blades. The building also facilitates a full‐scale 50 kW biomass-fueled, grid‐connected generator and a vehicle hoist of NVH experimentation.
In addition to the state-of-the art combustion vessel laboratory, the facility includes an air compressor room, a gas storage room, a mixing vessel enclosure, an equipment preparation room, and a control and monitoring room.
Location: Lahti Building (Hancock, MI)
Contact: Jeff Naber, Jaclyn Johnson
Automation in Manufacturing and Industrial Systems (AMIS) Lab
AMIS Lab conducts fundamental and applied research in the interdisciplinary fields of manufacturing and industrial systems to develop novel solutions to real-world problems. Our research focuses on developing perception, cognition, and human-interactive solutions for automation to further advance industrial systems and society.
- Universal Human-Machine Interface with Augmented Reality for Heterogenous Robots
- Explainable Artificial Intelligence (XAI) for Production Operators
- Intelligent Clustering of Big Data for Manufacturing Sustainability
- Standardizing and Evaluating Datasets for Automated Driving
Location: MEEM 128
Contact: Vinh Nguyen
Complex Fluids and Active Matter Lab
A fascinating class of problems in contemporary fluid mechanics involves the interplay between dynamic boundaries and fluid flows. The study of these problems usually requires accommodating several time and length scales. Moreover, they often involve complex geometries in which mechanical, chemical, and transport phenomena are coupled.
Contact: MAE Dept
Composite Materials Laboratory
The Composite Materials Laboratory conducts research on improving mechanical, thermal, and electrical properties of composites through the use of innovative processing techniques and nano-scale reinforcement. The lab is closely involved with the Institute for Ultra-Strong Composites (US-COMP), which is a NASA Space Technology Research Institute focused on developing novel ultra-strong and lightweight structural materials for use in deep space exploration.
The lab involves researchers in chemical engineering, materials science and engineering, and mechanical engineering.
Contact: Gregory M. Odegard or Paul G. Sanders
Computational Mechanics and Machine Learning Lab
We draw ideas from diverse disciplines such as computational mechanics, applied mathematics, and machine learning to model complex deformation of two-dimensional materials, model failure of materials, couple atomistic and continuum methods, solve inverse problems, accelerate material design, and quantify uncertainty. We have access to Superior HPC shared facility at MTU. We have four high performance Dell Precision Tower Workstations at our computational lab.
Location: High-Performance Computing Facility
Contact: Susanta Ghosh
Dynamics and Intelligent Systems (DIS) Group
We aim to understand dynamics behaviors of structures and systems and enable intelligent engineering systems. Our specific research includes Sensing, Modeling, Analysis, and Control of dynamic structures and systems, spanning the broad areas of system identification and control and experimental and computational mechanics, combining approaches from machine (deep) learning and computer vision with optical and acoustical tools.
Contact:
Great Lakes Energy Group
Like the warming climate, the electricity grid is changing rapidly and in ways that are not entirely predictable. We seek to understand how these concurrent changes affect the built environment and natural environment. We are engineers that are engaged and curious about the ecological and social interconnections of engineered systems.
Contact: Ana Dyreson
Intelligent Robotics and System Optimization Laboratory (IRoSOL)
The IRoSOL group aims to advance operational strategies for multiple heterogeneous autonomous vehicle systems with effective global coordination of the vehicles and local control of each vehicle. Our research focuses on real-time action for coordinating multiple heterogeneous robotic systems in various applications, such as surveillance, monitoring, search and rescue, power generation, transportation, and manufacturing.
Location: MEEM 301
Contact: Jung Yun Bae
Ion Space Propulsion Lab
The focus of the Ion Space Propulsion Lab (Isp Lab) is to develop and study next-generation thruster systems that use electrical energy to propel spacecraft. Electromagnetic forces are used to manipulate and exhaust ionized gases, producing reactive forces on in-space vehicles. The so-called “plasma thrusters” can only operate in the vacuum of space, so the Isp Lab maintains large, space-simulation chambers that enable ground-based testing of full-scale flight systems.
Current projects include xenon and magnesium Hall-effect thrusters that are used to raise the orbits of geostationary communications satellites, arcjets that are used to maintain orbits against gravitational perturbations, and electrospray microthrusters that are used to maneuver cell-phone-sized nanosatellites.
Location: MEEM B007C
Contact: Lyon (Brad) King
Mechanics, Acoustics, and Dynamics Lab (MADLab)
MADLab is an engineering research lab focused on understanding the fundamental mechanics of advanced structured material systems and leveraging this understanding to create new technologies for aerospace and mechanical applications.
Location: MEEM 501
Contact: Bhisham Sharma
Mechanics and Modeling of Advanced Materials Lab
Focus areas include micro-architectured polymeric material, oxidative aging in polymers, phase-field fracture of polymers, polymer curing-process modeling, and phase-field fracture of chemically strengthened glass.
Contact: Trisha Sain
Micro Electrical and Optical Sensing (µ-EOS) Lab
The µ-EOS Lab focuses on developing optical and electrical diagnostics of cellular physiological changes such as proliferation, migration, apoptosis, and so on. In addition to the opto-electrical examination of cells, this lab also works on micro/nano-fabrications and microfluidics. This lab is well equipped with dark room facility ready for fluorescent imaging. This lab currently holds two microscopies equipped with bright field, phase contrast, interference reflection, total internal reflection fluorescence, and epi-fluorescence optical components with help of the state of art 'electron multiplying charge coupled device (EMCCD) which allows very low intensity measurement. Another primary portion of this lab is the 'micro-impedance system', which consists of an SR830 lock-in amplifier, SCXI-1331 switch, DAQ board, along with other resistors. The corresponding data acquisition and analysis has been implemented for this system using LabVIEW software. Those optical and electrical capabilities are employed to develop a dynamic microfluidic cellular environment system, to examine the dynamic morphological evolution of cells, and to detect transport rates of various proteins in a live cell. In addition to the opto-electrical examination of cells, this lab also works on micro/nano-fabrications, microscale heat transfer (thin film evaporation), and microfluidics.
Soft Lithography Laboratory
The Soft Lithography Lab was being established in order to facilitate rapid fabrication of microfluidic systems in polydimethylsiloxane (PDMS), a soft silicon material. This lab is a departmental facility that includes a benchtop fume hood and a walk-in fumehood. Microchannel networks are fabricated by producing a negative of the microfluidic channels using a photoresist, the spin coater, a mask and the UV lamp. The PDMS can be cast and cured over the channel negative easily maintaining dimensions as small as 5 micrometers. Once cured, the PDMS block having the microchannels can be pealed off of the photoresist and placed in the plasma cleaner with another material (glass, plastic or PDMS) where the surfaces are ionized. The ionization takes only a few minutes, then the PDMS with the channels can be bonded to the second material by placing the materials in contact. A complex network of microchannels can be fabricated and bonded within an afternoon.
Cell Culture Room
This lab is open to our department faculty and students. This room owns autoclave, -20 and -80°C freezer, refrigerators, refrigerators, balance, vortex mixer, CO2 incubators, and laminar flow culture hood.
Location: MEEM 1002 (Main Lab), MEEM 1005 (Photolithography), MEEM 1006 (Cell Culture Room)
Contact: Chang Kyoung Choi
Mobile Lab
The Mobile Lab travels the country, providing hands-on professional-development training for engineers, technicians, and managers, as well as STEM outreach opportunities. On campus, the Mobile Lab is used for several Michigan Tech courses.
The basis of the Mobile Lab is a semitrailer with an expandable side, providing a comfortable, climate-controlled classroom. The lab includes two fully functional powertrain test cells. The test cells can be configured with spark-ignited or diesel engines or electric motors and can be set up to function as a hybrid powertrain. The test cells use AC dynamometers and include instrumentation for combustion and emissions analysis. The embedded control systems are used for rapid prototyping, and the cells can run fully automated. A fleet of twenty instrumented light-, medium-, and heavy-duty test vehicles and a vehicle-chassis dynamometer accompany the Mobile Lab.
The Mobile Lab provides over two dozen hands-on professional-development short courses at the customer’s location. Courses are available in electric machines and power electronics, batteries, engines, controls, instrumentation, data processing, and other areas. Custom course requests are always welcome.
Location: Variable
Contact: Jeremy Worm
Nanoindentation and Atomic Force Microscope Lab
A nanoindenter is a low-load indentation system for acquiring mechanical characterization data at the submicron scale. A diamond tip is used for the indentation. Given the known geometry of the diamond indenter tip, the depth of an indentation yields the area of contact between the tip and material being indented. Making an indentation with a controlled force, while continuously monitoring the displacement of the indenter, produces data from which hardness, modulus of elasticity, fracture behavior, and other mechanical properties can be calculated. The Nanoindentation Lab houses the Agilent NanoIndenter XPS system with the following options:
- Continuous Stiffness Measurement
- Lateral Force Measurement
- High-Load System
- High-Performance Table
- Dynamic Contact Module
- Nanopositioning Stage and Nano-Vision Microscope
Agilent NanoIndenter XPS System Specifications | |
---|---|
Displacement Resolution | <0.01 nm (XP), 0.0002 nm (DCM) |
Maximum Load | 500 mN (XP), 1 kg (XP-High Load), 10 mN (DCM) |
Load Resolution | 50 nN (XP and XP-High Load), 1nN (DCM) |
Atomic Force Microscopy (AFM) is a Nobel Prize-winning technology that scans a sharp tip along the sample surface to resolve features down to subnanometer size (<10-9 m). In addition to the widely used tapping mode and contact mode, this system is equipped with the most-advanced nanomechanical-measurement modes (peak force and nanoindentation), as well as electrical conductivity, piezoresponse force microscopy, and liquid-imaging modules. Mechanical properties (e.g., Young’s modulus and adhesion) and electric properties (e.g., surface potential and conductance) can be monitored with high resolution.
Location: MEEM S005
Contact: MAE Dept
Nucor Metrology Center
The Nucor Metrology Center provides students with the resources to make highly accurate measurements for their project components. The lab features both traditional and leading-edge, industry-standard equipment, including calipers, micrometers, a flexible arm coordinate-measurement machine (CMM), optical microscope, microhardness testers, tachometers, strobometers, and infrared and thermal scanners. Nucor’s donation allowed for the purchase of a Leica DVM6 motorized digital microscope and a Hexagon Metrology absolute measurement arm, giving us the ability to do high-quality metrology measurements for part inspection.
Location: MEEM 101
Contact: Jason Blough
Planetary Surface Technology Development (PSTD) Lab
HuskyWorks
Projects
- NASA LuSTR 2020
- NASA T-REX
- NASA Watts on the Moon
- NASA Break the Ice
- NASA ESI
- NASA RedWater
- NASA GCD MRE
- HOPLITE
- NASA CLASS
Facilities
- Dusty Thermal Vacuum Chamber (DTVAC)
- Lunar Simulant Sandbox
- IRGO
- Mini Thermal Vacuum Chamber (MTVAC)
- Regolith Freezing and Heating Containers
- AR Mapping Sandbox
- Industrial Robotic Arm
Location: MEEM 701A
Contact: Paul van Susante
Solvent-targeted Recovery and Precipitation (STRAP) Application
STRAP can restore contaminated plastics, including foodgrade materials, to their original state for reuse. Applications of STRAP include green solvents, municipal solid waste, and disposable face masks.
Location: APS Labs
Contact: Ezra Bar-Ziv
Wave Tank
MTU Wave is the collaborative wave tank laboratory at Michigan Tech dedicated to advancing research and development in the field of floating offshore technologies. It features a 10 m x 3 m x 1 m Edinburgh Designs wave tank with eight independently controlled paddles with position and force feedback to generate desired wave fields propagating towards an adjustable 3 m long curved high-density, polyethylene, energy-adsorbing beach. Ideal for scientists and engineers studying floating structures.
Location: MEEM S001, S001A
Contact: Gordon G. Parker